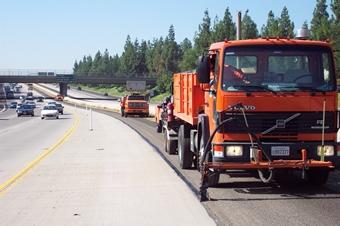
Longitudinal Crack Sealing
Longitudinal Crack Sealing Video
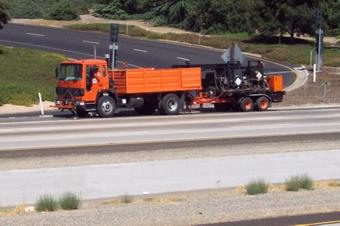
The Longitudinal Crack Sealing Machine (LCSM) program is dedicated to the development of automated sealing machines for relatively continuous longitudinal cracks, such as those that occur between a concrete lane and asphalt shoulders. The machine pictured here is the second generation Longitudinal Crack Sealing Machine (LCSM2) operated by Caltrans Maintenance crews in the Fresno area.
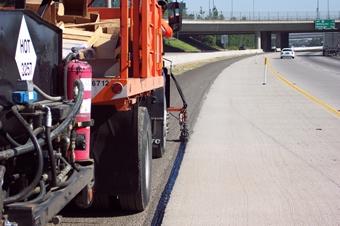
The LCSM2 enables a highway worker to seal longitudinal pavement cracks and joints with hot applied sealant from inside the relative safety of the truck cab. No longer do workers have to be exposed to direct traffic in longitudinal sealing operations as in the traditional manual application procedure. The driver controls the entire sealing process from within the truck cab while a support worker is typically utilized to load the sealant blocks into the kettle. Use of the LCSM2 also dramatically increases seal production rate, primarily by eliminating the strenuous nature of the operation.
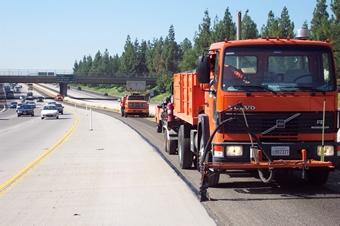
The driver/operator remotely deploys the application head to the pavement, steers the truck along the crack, controls sealing speed with the accelerator petal, and remotely controls the sealant flow with a hand controller. The shoe pulls along a reservoir of sealant that overcomes the random change in crack size. A display screen in the cab relays machine status information to the driver.
Second Generation Longitudinal Crack Sealing Machine
LCSM2 Caltans Field Deployment
The LCSM2 was placed in service with Caltrans Maintenance in March of 2000. The machine proved to be very popular with Caltrans maintenance crews and was primarily operated in Caltrans Districts 6 and 11. Initially, longitudinal crack sealing operations were only conducted in fixed temporary lane closures. Caltrans crews began to operate the LCSM2 from the shoulder of the highway sealing edge cracks next to live lanes. This technique provided additional cost benefits by saving closure costs. Other Caltrans crews pioneered the technique of hot sealant transfer to extend seal production capacities.
In 2002, AHMCT was contracted by Caltrans to design the next generation longitudinal sealing machine while the LCSM2 was being successfully operated on the highway. The goal of the third generation LCSM design was to incorporate many new features requested by LCSM2 users in the field. A dramatically increased hot sealant supply and moving lane closure operation were the biggest issues to be adressed. The new machine is called the Transfer Tank Longitudinal Sealer(TTLS) and is scheduled to be field tested with Caltrans in Summer 2005.
Cost and Safety Benefit
The District 11, Chula Vista Travelway Crew has reported some cost data when using the LCSM vs. Hand Applied Operation.
Distance Compared: 32 miles along Interstate-5
LCSM | Hand Applied | |
Number of employees | 3 | 4 |
Average miles per day | 3.5 | 0.8 |
Work days | 9 | 40 |
Bare rate cost | $4,017 | $23,820 |
Closures | NO | YES |
Employees on foot | NO | YES |
- LCSM — In 17 days, 62 miles of AC/PCC joint line was sealed on Routes 5, 52, and 125.
- Hand Applied Method — The same amount of miles sealed would have required 77.5 days, 78 lane closures, and 465 hours of exposure of employees on foot to traffic.
Injuries possibly avoided by using the LCSM:
- There have been a total of 76 injuries in the last 10 years associated with rubber crack sealing.
- 27 employee injuries resulted from applying rubberized product on foot.
- 12 employee injuries resulted from loading material.
- 39 employee injuries reported that were not related to just rubberized crack sealing.